Techniques de fabrication Tubes en verre
La fabrication industrielle automatisée des tubes en verre est réalisée selon le procédé général présenté ci‐dessous. Elle répond à un process rigoureux et fait l’objet de multiples contrôles qualité. Ces tubes sont principalement destinés au marché pharmaceutique.
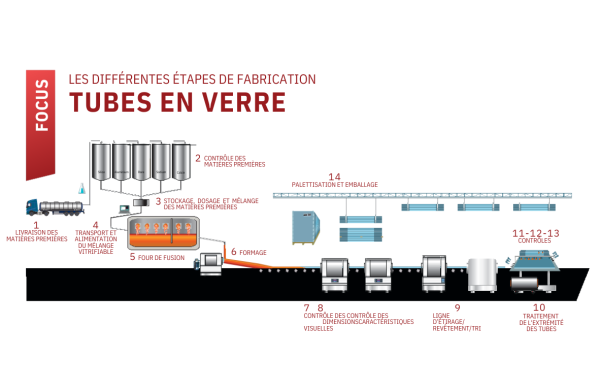
1/ Livraison des matières premières
Les livraisons de matières premières sont quotidiennes. Elles arrivent en camions étanches ou en big bags
2/ Contrôle des matières premières
Les matières premières sont échantillonnées et analysées. Un contrôle permet de vérifier la correspondance entre spécifications et les matières premières.
3/ Stockage, dosage et mélange de matières premières
Des systèmes de dosage et de mélange entièrement automatisés garantissent une stabilité élevée du processus, qui se traduit par des propriétés physico-chimiques constantes.
4/ Transport et alimentation du mélange vitrifiable
Le mélange vitrifiable est transporté via des pipelines revêtus de céramique. L’alimentation en continu du mélange garantit le faible pourcentage de défauts visuels.
5/ Four de fusion
La composition est fondue à haute température dans un four de fusion autour de 1600°C.
6/ Formage
Le verre fondu recouvre en continu le mandrin Danner. Tandis que de l’air filtré est soufflé, un tube se forme à l’extrémité du mandrin et s’étire en continu.
7/ Contrôle des caractéristiques dimensionnelles
Des systèmes de contrôle permettent d’assurer un suivi des caractéristiques dimensionnelles et de réguler le processus de production. Les données mesurées sont transférées au système de gestion qui les intègrent en base de données.
8/ Contrôle des caractéristiques visuelles
Des systèmes de contrôle permettent d’assurer un suivi de la qualité visuelle des produits et de réguler le processus de production. Les données mesurées sont transférées au système de gestion qui les intègrent en base de données.
9/ Ligne d’étirage/revêtement/tri
Les tubes sont étirés en continu. A cette étape, il est possible d’ajouter un revêtement anti-rayures. Les tubes sont ensuite triés et découpés sur la base des données fournies par les systèmes de contrôle.
10/ Traitement de l’extrémité des tubes/Limitation des particules
Les extrémités des tubes sont vitrifiées. Une finition appropriée des extrémités des tubes est apportée à cette étape (par ex. rebrûlage, rétractation…). Un système permet de limiter la quantité de particules.
11/ Contrôle de l’extrémité des tubes
Grâce à une caméra, différents contrôles sont effectués : finition des extrémités conforme, perpendicularité, amorces, trou… Les données mesurées sont transférées au système de gestion des données.
12/ Contrôle des caractéristiques dimensionnelles de chaque tube
Un nouveau contrôle permet de vérifier les caractéristiques dimensionnelles de chaque tube : diamètre extérieur, rectitude, circularité… Les données mesurées sont transférées au système de gestion des données.
13/ Autocontrôle de l’opérateur
L’autocontrôle régulier des opérateurs permet de vérifier les données mesurées par le système. Les paramètres suivants sont vérifiés : diamètres extérieurs et intérieurs, épaisseur de paroi, différence d’épaisseur de paroi, longueur, perpendicularité, circularité, rectitude, etc.
Des contrôles complémentaires des propriétés chimiques et physiques sont également effectués en laboratoire.
14/ Palettisation et emballage
Les tubes sont ensuite emballés et sont prêts à être expédiés aux clients.