Techniques de fabrication Verre d'emballage
La fabrication industrielle automatisée des bouteilles, pots et flacons en verre est réalisée selon le procédé général présenté ci‐dessous. Elle répond à un process rigoureux et fait l’objet de multiples contrôles qualité. Le mélange de matières premières et de calcin est fondu en continu dans un four à 1500°. Entre l’entrée du mélange et la sortie du verre en fusion, 24 heures s’écoulent.
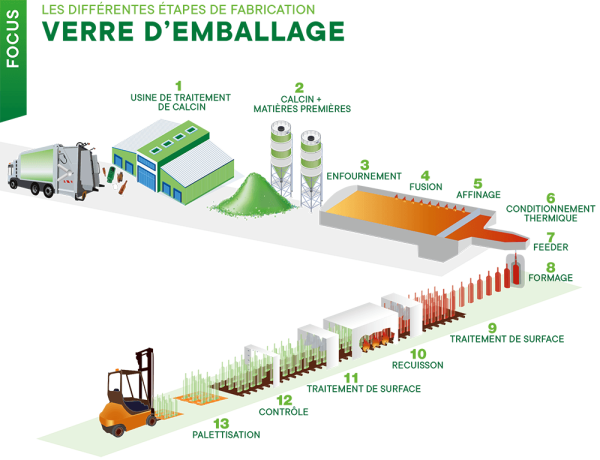
1/ Usine de traitement de calcin
Le verre issu de la collecte est acheminé dans une usine de traitement, où est débarrassé de ses impuretés. Devenu calcin, il est prêt à redevenir du verre.
2/ La composition
Sable, calcaire, carbonate de sodium entrent dans la composition du verre. Ces composants peuvent être remplacés par du calcin – verre collecté, trié et nettoyé. Les matières premières sont mélangées dans l’atelier de composition, selon des proportions soigneusement définies.
3/ L’enfournement
Le mélange est ensuite déversé dans le four.
4/ La fusion
Le four est composé d’une cuve en matériaux réfractaires dans laquelle la composition est fondue à haute température, entre 1300° C et 1 550° C. C’est la fusion.
5/ L’affinage
C’est la deuxième étape de la fonte du verre dans les fours de production. Il a lieu entre 1450 et 1530°C et sert à supprimer les impuretés dégagées lors de la fusion pour obtenir une matière homogène.
6/ Le conditionnement thermique
Il s’agit de la troisième étape de la fonte du verre. C’est l’obtention de la température exigée pour l’alimentation du verre aux ouvreaux des feeders.
7/ Le feeder
Le feeder est un long canal qui amène le verre en fusion du bassin du four aux machines de formage.
8/ Le formage
La goutte de verre en fusion, appelée paraison, est soufflée dans un moule « ébaucheur » puis dans un moule « finisseur » placé sur la machine qui fabrique les emballages.
9/ Le traitement de surface (à chaud)
La résistance mécanique dépend surtout de la présence ou non de défauts de surface que le verrier va chercher à éviter, notamment par des traitements de surface protecteurs. Le traitement dit « à chaud » (560°C) est déposé en phase vapeur entre la machine de fabrication et l’arche de recuisson. Il a pour but de revêtir la surface extérieure des emballages en verre afin d’augmenter sa dureté et de permettre un bon accrochage du deuxième traitement déposé après l’arche de recuisson.
10/ La recuisson
Le verre doit être refroidi dans des conditions spéciales pour éviter les écarts trop brusques de température qui rendraient l’emballage fragile : c’est le « recuit » réalisé dans un arche de recuisson.
11/ Le traitement de surface (à froid)
Le traitement « à froid » par pulvérisation, pour les produits les plus efficaces, consiste à déposer un lubrifiant (antirayure) facilitant le glissement face à la rayure. Ce lubrifiant est généralement à base de polyéthylène (épaisseur environ 1 micron).
12/ Le contrôle des emballages
La qualité des emballages est contrôlée par différentes machines. Ceux qui présentent des défauts sont éjectés et transformés de nouveau en calcin.
13/ La palettisation
Afin d’assurer la sécurité des emballages en verre, ils sont déposés sur des palettes puis houssés pour être livrés à l’utilisateur final.